TECHNOLOGIES
TECHNOLOGIES FOR GAS PROCESS MODULES
Celerity has developed three proprietary technologies that are revolutionizing gas process modules. They are: MultiFlo® technology, PTI technology, and Step® technology.
MultiFlo® Technology

MultiFlo® technology incorporates a linear sensor by-pass subsystem with sophisticated physics-based algorithms, to enable mass flow controller (MFC) reconfiguration for over 180 different gases and mixtures without special test fixtures or expensive calibration gases. MultiFlo® technology integrates sensor calibration, sensor response filters, and valve control parameters to compensate for unique gas properties. This technology integration allows the MFC to maintain original calibration accuracy and eliminate overshoot and oscillation when it is configured for a new process gas.
In addition, our MultiFlo® flow control technology significantly reduces our manufacturing cycle time for gas delivery modules and instruments. Moreover, thanks to the flexibility built into our physics-based approach to modeling gas characteristics, we observe that our MFCs cover 85 percent of all gas delivery applications with nine configurable "blanks." These nine standard configurations eliminate the requirement for stocking hundreds of unique MFC part numbers and therefore reduce inventory carrying costs. Furthermore, MultiFlo® technology reduces average replacement time from more than four hours to minutes for conventional MFCs, plus there are no reconfiguration costs associated with live gas re-calibration. Instead of "make to order," you simply "configure to order" from stock. This enables our customers to cost effectively maintain the inventory needed to rapidly deliver replacement parts on demand and significantly reduce equipment downtime without sacrificing performance. MultiFlo® provides consistent and accurate gas delivery for critical process gas and flow setpoints. Best of all, this unique solution's sound approach easily ports to all our products, making it equally applicable to the next-generation of flow technology.
MultiFlo® benefits include:
- Dramatically reduces inventory requirements
- Nine part numbers cover 85% of gases and ranges used in a typical fab (from 3 sccm to 30 slm)
- Enables in situ configuration within a few minutes
- Reduces down-time
- Reduces cost of ownership
PTI Technology

Embedded in our next-generation gas modules, pressure transient insensitive, or PTI, technology improves flow control and output stability by minimizing the damaging effects of pressure fluctuations. By integrating a pressure transducer with proven mass flow technology, PTI technology stabilizes flow output for a constant flow rate no matter what pressure changes occur up or down stream. It eliminates today's gas delivery challenges such as "cross-talk" and the "first wafer effect" and removes the need for additional line pressure regulation. PTI technology allows us to engineer out complex components, reduce seals, shorten purge cycle requirements, and decrease the likelihood of failures - all of which means less downtime.
PTI technology significantly reduces process stabilization time in the presence of pressure transients. Customers report a reduction in sidewall void formation, an improvement in process uniformity, increased process throughput and a five-fold improvement in process stabilization time. This ensures a consistent response independent of inlet pressure. Finally, PTI technology benefits customers with lower cost of ownership, by enabling a smaller footprint for the gas delivery system and improving throughput and stabilization times for flow response.
PTI benefits include:
- Integrated pressure transducer eliminates cross-talk
- Eliminates need for line pressure regulation
- Reduces down-time
- Provides fast response
- Reduces footprint
- Reduces cost of ownership
Performance Benefits with PTI Technology:
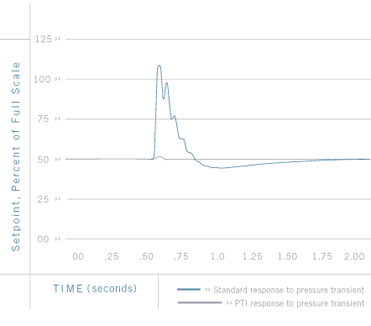
Step® Technology

Celerity's embedded Step® technology enables fast response to control setpoints. Step® utilizes a high-speed digital signal processor, or DSP, and employs an optimized sensor drive circuit to deliver industry-leading flow stabilization time. For low-flow applications, it supports faster throughput by reducing typical process stabilization times by three to eight seconds per device layer. It also enables fast-switching processes employed in micro electro mechanical systems (MEMS) and critical device manufacturing. Our Step® technology's ability to reduce flow stabilization times makes gases available at the desired rate more quickly, leading to better tool utilization, higher throughput and improved cost of ownership.
Step benefits include:
- Faster throughput for low flow applications (i.e. reduces typical stabilization times from 3 to 8 seconds per device layer)
- Enables fast-switching processes (such as the Bosch process) employed in MEMS and critical device manufacturing
Performance Benefits with Step Technology:
